Оптоволоконный Лазерный Режущий Станок
Прямая Продажа Без Посредников
Мы предлагаем волоконные лазерные станки для резки с диапазоном мощности от 1000 до 40000 Вт, способные резать углеродистую сталь более 30 мм и нержавеющую сталь более 25 мм. Лазерные источники и режущие головы - это мировые бренды, такие как Precitec, Raytools, AU3Tech, WSX; OSPRI лазерные источники IPG, Raycus, JPT, Max photonics и другие. Мы также предлагаем экономичные решения, такие как использование лазеров Raycus и лазерных режущих головок WSX китайского производства.
Эффективность лазерной резки
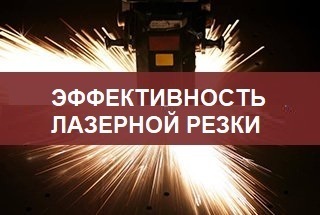
В настоящее время применение станков для лазерной резки становится все более обширным, особенно в области обработки изделий из листового металла .
Лазерная обработка имеет преимущества высокой точности обработки, хорошего качества поверхности, низкого шума обработки и небольшой вибрации оборудования. Однако лазерная резка также имеет недостатки, заключающиеся в низкой скорости обработки, низком коэффициенте использования материала и высокой стоимости комплексной обработки.
Станок для лазерной резки использует принцип бесконтактной обработки. По сравнению с обычной многопозиционной обработкой пуансонов, специальная форма не требуется, поэтому объем и условия ее обработки ограничены.
Согласно требованиям к дизайну изделия сложную форму можно вырезать по желанию. Он подходит для единичного пробного производства и мелкосерийного производства, что позволяет быстро удовлетворить стремление клиентов к индивидуализированной продукции. При обработке толстых листов преимущества лазерной резки более очевидны.
Толщина резки стального листа составляет более 20 мм, обычные многопозиционные прессы могут обрабатывать только 3 ~ 8 мм. Поскольку станок для лазерной резки использует движущуюся лазерную режущую головку для обработки листа, поэтому он имеет более длинный ход вперед и назад.
По сравнению с многопозиционной штамповочной машиной скорость обработки низкая, общее время обработки велико, эффективность низкая, а дозировка вспомогательного газа большая.
Таким образом, комплексная стоимость лазерной резки намного выше, чем стоимость штамповки. Как сократить время лазерной резки и повысить эффективность лазерной резки - это забота многих производителей. Повышается эффективность и экономическая выгода станка для лазерной резки, что в основном связано с сокращением времени лазерной резки и повышением коэффициента использования листа.
Необходимо не только изучить кратчайший путь лазерной резки по воздуху, но и изучить такие проблемы, как время сверления, пауза резки и раскрой.
Анализ
Время резки
Путь лазерной резки можно разделить на две части, включая путь резки и технологический путь для удаления или разделения материала.
Путь резания - это эффективный рабочий путь, затраченное время - это эффективное время резания, пустой ход - холостой путь, а затраченное время - недействительное рабочее время.
Для 1 станка лазерной резки с ЧПУ при использовании обрабатываемых деталей максимальной мощности эффективная скорость резки гарантирована, если гарантировано и качество.
Основным методом является повышение эффективности резки и сокращение времени некорректной резки и уменьшение длины пути резки.
Кроме того, соответствующая настройка параметров процесса резки и выбор различных методов перфорации также может сэкономить время на обработку резки.
В случае пробивки отверстий, таких как регулировка внешнего светового пути, собирающего луча, вертикальная регулировка и т.д.
Использование листового металла
Процесс лазерной резки листа делится на две части, включая компоненты и остаточные материалы.
Заготовки, вырезанные по чертежам, действительно полезные, а остальное - нестандартное, обычно в качестве мусора.
Следовательно, эффективный коэффициент использования материала для лазерной резки = площадь полезных частей / общая площадь листа * 100%.
Чтобы улучшить коэффициент использования листа, мы должны уменьшить количество остаточного материала после лазерной резки.
Теперь оборудование для лазерной резки можно использовать для оптимизации функции раскроя. Это основной способ уменьшить расстояние между резками и кромку различных деталей.
Конечно, также можно выбрать небольшую пластину для исходного материала в соответствии с размером заготовки или по фактическому размеру детали, чтобы сделать пластину нестандартного размера, чтобы улучшить фактическое использование пластины.
Решение
Программное обеспечение для автономного программирования станка для лазерной резки используется для оптимизации настройки листового материала и процесса, чтобы повысить коэффициент использования и эффективность резки.
В основном принимаются следующие меры:
При раскладке используйте заимствованную кромку и общую кромку
Детали с правильной формой принимают заимствованную кромку и общую кромку при раскрое.
При резке одна кромка двух частей является общей кромкой, поэтому путь резания будет значительно сокращен, что сократит время резания.
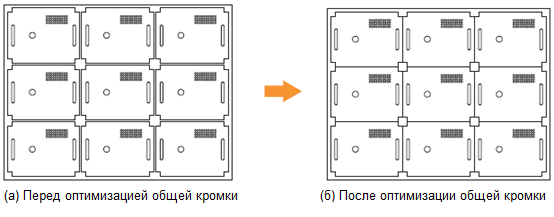
На одном листе металла нельзя сделать так, чтобы все детали имели одну кромку. Как правило, рекомендуется использовать 2 ~ 4 части как группу для разделения края.
В противном случае все детали имеют общую кромку, что приведет к нестабильности деталей на столе.
Поскольку готовые детали будут переворачиваться, детали будут обрабатываться по краю деталей готового продукта, что будет мешать обработке и скорее всего повредит режущую башку.
Чтобы повысить точность конечной детали, можно использовать метод перемычки при резке с общей кромкой, то есть для создания точных и сверхточных вырезов деталей.
Расстояние - это диаметр лазерного пучка.
Согласно статистике, фактическая траектория резания может быть уменьшена на 30%, а коэффициент использования материала увеличен на 8%, если использовать общую режущую кромку.
Уменьшите подъем режущей головки
Обычно машина поднимается на определенную высоту после вырезания контура, а затем перемещается в положение резки следующего контура для протыкания (пирсинга) и резки.
Это делается для предотвращения столкновения с обрезанной деталью при перемещении режущей головки от текущего профиля к следующему профилю резания.
Однако, как только траектория резания режущей головки оптимизирована или используется контур микросоединения, подъемное движение режущей головки может быть сокращено до минимума ил удалено для повышения эффективности лазерного раскроя.
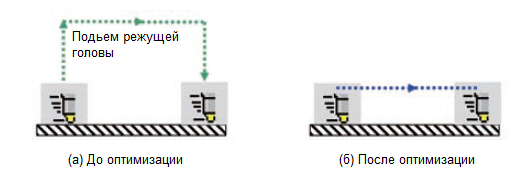
На рисунке (а) выше показано подъемное действие режущей головки.
На рисунке (б) показано, что режущая головка не поднимается после оптимизации и настройки в программном обеспечении. Переходите непосредственно к позиции резки следующего контура.
Обратите внимание, что после использования вышеуказанного метода оптимизации вы должны обратить внимание на траекторию движения режущей головки.
Другими словами, режущая головка не может проходить по готовому контуру.
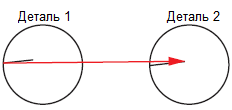
Традиционная траектория лазерной резки
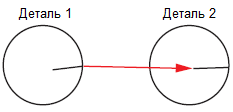
Оптимизированная траектория резки лазерной головки
Оптимизация траектории резания при запуске процесса лазерного прокола отверстий
Перед лазерной резкой отверстия сначала проделайте отверстие в пластине.
После того, как материал облучается непрерывным лазером, в центре образуется кратер, и расплавленный материал удаляется рабочим потоком воздуха или иного газа с помощью лазерного луча, образуя отверстие.
Это отверстие похоже на отверстие с резьбой, как будто после метчика.
Лазерный луч используется для контурной резки в начальной точке обработки.
Обычно направление линии лазерного луча траектории полета перпендикулярно касательному направлению контура реза обрабатываемой детали.
На качество лазерного прокола влияет множество факторов.
Он должен быть основан на принципе и характеристиках бурения, а параметры бурения должны быть проанализированы и поняты для оптимизации технологии обработки.
Использовать разные технологии прокола и обработки для разных контуров деталей.
Режим прошивки станка для лазерной резки в основном включает следующие три вида:
(1) Без проколов (для тонких листов менее 1 мм)
(2) Обычный прокол, который является проколом в импульсном режиме, заключается в использовании импульсного лазера с высокой пиковой мощностью для плавления или испарения небольшого количества материала. Каждый импульс света производит только маленькие частицы испарения, которые постепенно послойно углубляются, поэтому для прокалывания толстой пластины требуется несколько секунд.
Преимущество в том, что качество прошивки высокое и соответственно качество резки тоже гарантировано.
Недостаток в том, что это занимает много времени и требует некоторого опыта отладки, а время прокола увеличивается с толщиной пластины.
(3) Быстрый прокол, а именно взрывная перфорация.
После непрерывного лазерного облучения материал образовывал ямку в центре.
Преимущество в том, что время прокола невелико.
Недостаток - большая перфорация. Неправильная установка положения повлияет на контур, что повлияет на качество резки.
Время прокола в пределах 1 секунды.
Однако перед настройкой быстрого прокола необходимо правильно отрегулировать длину линии разреза (отверстия для быстрого прокола имеют большую апертуру и шероховатую поверхность, что требует более длинных входных линий для правильного качества резки).
Оптимизация листового раскроя, сокращение отходов при резке листа
Из-за технологических потребностей детали обычно резервируются в области раскроя. Например, расстояние между деталями или расстояние внешнего контура листа.
Правильное уменьшение расстояния или использование общей кромки может быть использовано для рационального использования листа.
Заключение
Чтобы объяснить, как сократить время лазерной резки и повысить коэффициент использования листа, используйте оптимизацию при резке кромок, оптимизация листового материала, уменьшение подъема режущей головки и разумный выбор метода раскроя.
Посредством практической проверки всестороннее использование вышеуказанных методов может эффективно повысить эффективность работы, сократить отходы и повысить экономические выгоды.
Контакты
Телефон | +7(495)797-78-97 |
Адрес | ООО "АрматА", ИНН 7721482360, г. Москва, Рязанский проспект, д. 86/1 |
info@fiber-laser.ru | |
Доп. поле | Авторизованный дилер RayTools AG на территории РФ |
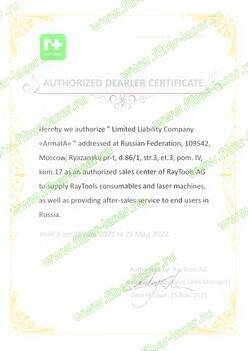