Оптоволоконный Лазерный Режущий Станок
Прямая Продажа Без Посредников
Мы предлагаем волоконные лазерные станки для резки с диапазоном мощности от 1000 до 40000 Вт, способные резать углеродистую сталь более 30 мм и нержавеющую сталь более 25 мм. Лазерные источники и режущие головы - это мировые бренды, такие как Precitec, Raytools, AU3Tech, WSX; OSPRI лазерные источники IPG, Raycus, JPT, Max photonics и другие. Мы также предлагаем экономичные решения, такие как использование лазеров Raycus и лазерных режущих головок WSX китайского производства.
Лазерная резка листового металла
(проблемы и их решения)
В процессе резки листового металла с помощью лазера часто возникают различные проблемы.
Чтобы обеспечить качество резания листа лазером, вот 7 общих проблем и 7 их общих решений:
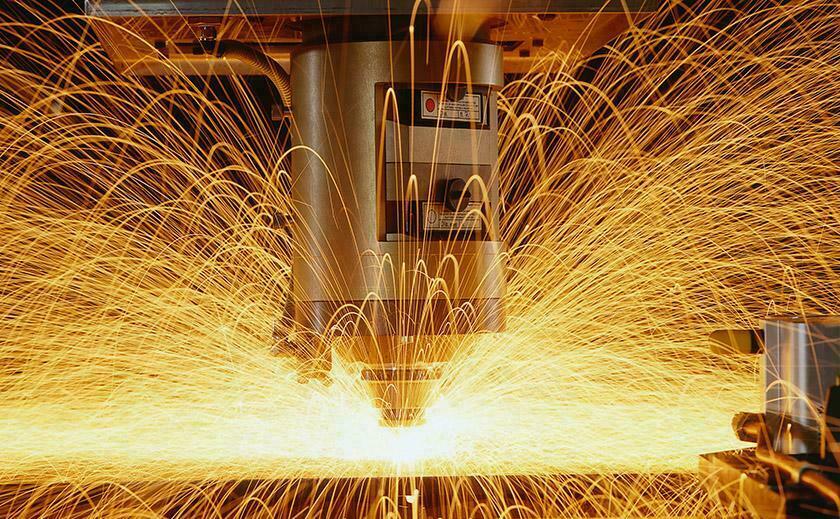
Технология режущей перфорации
Как правило, для любого вида технологии горячей термической резки необходимо просверлить небольшое отверстие в листовом металле, за исключением нескольких случаев, когда можно начать с края листа.
Предварительно в нем пробивали отверстие с помощью пуансона пресс-формы в лазерной штамповочной машине, затем лазер начинал прорезать отверстие.
Существует два основных метода лазерной резки без штамповочного устройства:
Струйная перфорация (Blasting)
Материал образовал яму в центре после непрерывного лазерного излучения, затем поток кислорода с лазерным лучом быстро выдувает расплавленный материал, образуя отверстие.
Размер обычного отверстия связан с толщиной пластины.
Средний диаметр струйной перфорации составляет половину толщины пластины. Поэтому отверстие перфорации более толстого листа струйной обработкой большое и не круглое.
Этот метод не должен использоваться на деталях с высокой точностью обработки и может использоваться только для зпаготовительных операций.
Кроме того, давление кислорода, используемое в перфорации, такое же, как и при резке, и оно имеет слишком много брызг.
Импульсная перфорация (Pulse)
Импульсный лазер с пиковой мощностью используется для расплавления или испарения небольшого количества материала.
Обычный воздух или азот используются в качестве вспомогательного газа для уменьшения расширения отверстия из-за экзотермического окисления.
Давление газа меньше давления кислорода при резке.
Каждый импульсный лазер производит только небольшие частицы, которые выбрасываются, а затем обработка постепенно углубляется.
Таким образом, требуется несколько секунд, чтобы толстая пластина прокололась.
Как только перфорация завершена, вспомогательный газ немедленно заменяется кислородом для резки.
Таким образом, диаметр перфорации меньше, а качество перфорации лучше, чем у струйной обработки.
Для этого лазер должен иметь не только более высокую выходную мощность, но и пространственно-временные характеристики луча.
Поэтому общий поток CO2-лазера не может соответствовать требованиям лазерной резки.
Кроме того, импульсная перфорация также должна иметь надежную систему контроля газа для реализации контроля типа газа, переключения давления газа и времени перфорации.
Для получения качественного разреза в случае импульсной перфорации следует серьезно отнестись к технологии перехода от импульсной перфорации заготовки к непрерывной резке заготовки.
Теоретически условия резания ускоряющего периода, такие как фокусное расстояние, положение сопла и давление газа, обычно могут быть изменены. Но вряд ли вышеперечисленные условия будут изменены за слишком короткое время.
В промышленном производстве более реалистично принять метод изменения средней мощности лазера. Специфический метод заключается в изменении ширины импульса, частоты импульса или изменении ширины и частоты импульса одновременно.
Фактические результаты показывают, что третий эффект является лучшим.
Анализ деформации резания мелких отверстий
(малого диаметра и толщины)
Это связано с тем, что режущий лазер (только для мощного лазера) применяется не методом струйной перфорации при обработке отверстия, а с использованием импульсной перфорации (мягкий прокол).
Это приводит к тому, что лазерная энергия слишком концентрируется на небольшой площади, обугливает необработанную область, что приводит к деформации отверстия и влияет на качество обработки.
В это время мы должны изменить метод импульсной перфорации (мягкий прокол) на струйную перфорацию (обычный прокол) в процедуре обработки, чтобы решить эту проблему.
Для менее мощных станков лазерной резки верно обратное. Необходимо использовать импульсную перфорацию для достижения лучшей отделки поверхности при резке небольших отверстий.
Заготовка получается с заусенцами при резке низкоуглеродистой стали, как это решить.
В соответствии с принципом работы и конструкции CO2 лазера, в качестве основных причин возникновения заусенцев на заготовке выявляются следующие причины:
- Лазерный фокус находится не в правильном положении. Тест положения фокуса необходим для регулировки смещения в соответствии с фокусом.
- Выходная мощность лазера недостаточна. Необходимо проверить, правильно ли работает лазерный источник.
- Скорость линейного реза слишком медленная и нуждается в увеличении;
- Чистота режущего газа недостаточна, необходимо обеспечить высокое качество режущего газа;
- Миграция лазерного фокуса. Требуется проверка местоположения фокуса и настройка в соответствии со смещением фокуса.
- Нестабильность возникает из-за длительного времени работы лазерной головы. Вам нужно выключить лазер и перезапустить его.
Анализ неполного режущего состояния лазера.
Проведя анализ, можно обнаружить, что основными условиями получения нестабильной обработки являются следующие ситуации:
- Выбор лазерного сопла не соответствует толщине пластины;
- Скорость лазерной резки слишком высока, и линейная скорость должна быть уменьшена. Кроме того, важно отметить, что при резке листа из углеродистой стали 5 мм с помощью лазерного станка необходимо заменить лазерную линзу с фокусным расстоянием 7,5 дюйма.
Решение для ненормальной искры, появляющейся при резке низкоуглеродистой стали.
Такая ситуация скажется на качестве режущего сечения деталей.
В это время, когда другие параметры находятся в норме, следует учитывать следующие ситуации:
- Произошла потеря лазерного сопла и сопло должно быть вовремя заменено. При условии, что новое сопло не заменяется, давление режущего рабочего газа должно быть увеличено.
- Резьба на стыке сопла и лазерной режущей головки ослаблена. В этом случае обработку следует немедленно остановить, проверить состояние соединения лазерной головки и восстановить резьбу винта.
Выбор точек прокола при лазерной резке.
Принцип работы лазерного луча при лазерной резке:
- В процессе обработки материал формируется в яму (колодец) в центре после непрерывного лазерного облучения.
- Затем рабочий поток воздуха с помощью лазерного луча быстро удалит расплавленный материал с образованием отверстия.
Это отверстие похоже на резьбовое отверстие. Лазерный луч берет это отверстие в качестве начальной точки обработки для контурной резки.
Обычно направление траектории лазерного луча на траектории полета перпендикулярно касательному направлению контура среза обрабатываемой детали. Поэтому за время проникновения лазерного луча в стальной лист, до прорезания контура, скорость резания будет иметь большое изменение в направлении вектора, то есть на 90 ° вращаться в направлении вектора.
Тангенциальное направление, перпендикулярное профилю реза, превращается в касательную линию, перекрывающуюся с контуром реза. А именно, угол с касательной контура равен 0 °
Это приведет к шероховатой поверхности среза на разрезанном участке обрабатываемого материала.
А происходит это главным образом потому, что за короткий промежуток времени изменения движения лазерного луча в направлении вектора направления происходят очень быстро.
Поэтому мы должны обратить внимание на этот аспект при использовании лазерной резки деталей.
Как правило, когда деталь не имеет требований к шероховатости для поверхностной резки, в программировании лазерной резки не будет установлено ручное управление, чтобы управляющее программное обеспечение могло автоматически генерировать точки прокола.
Однако, когда конструкция имеет высокие требования к шероховатости режущего сечения обрабатываемых деталей, важно принять во внимание эту проблему.
Обычно при подготовке программы лазерной резки необходимо вручную регулировать исходное положение лазерного луча, то есть ручное управление точкой прокола.
Необходимо переместить точку прокола, полученную лазерной программой, в нужное разумное положение, чтобы удовлетворить требованиям точности поверхности обрабатываемых деталей.
Контакты
Телефон | +7(495)797-78-97 |
Адрес | ООО "АрматА", ИНН 7721482360, г. Москва, Рязанский проспект, д. 86/1 |
info@fiber-laser.ru | |
Доп. поле | Авторизованный дилер RayTools AG на территории РФ |
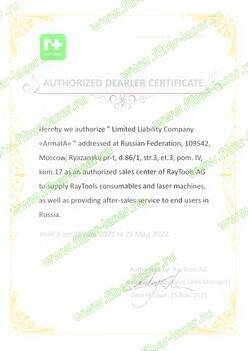