Оптоволоконная Лазерная Сварка
Прямая Продажа Без Посредников
Мы предлагаем волоконные лазерные сварочные аппараты для сваркиметаллов с диапазоном мощности от 1000 до 2000 Вт, способные cваривать углеродистую сталь более 5 мм и нержавеющую сталь более 3 мм толщиной. Лазерные источники и сварочные лазерные головы - это мировые бренды, такие как WSX; OSPRI, Hanwei, Qilin, KRD лазерные источники Raycus и JPT. Мы также предлагаем все расходники и комплектующие для лазерных сварочных аппаратов.
Сварка пластмассы с металлом
На примерах доказано, что металл и пластик могут быть высоконадежно “сварены” лазером.
Точнее, это должно быть “соединение”.
На рисунке 1 ниже дверь автомобиля усилена стеклопластиком.
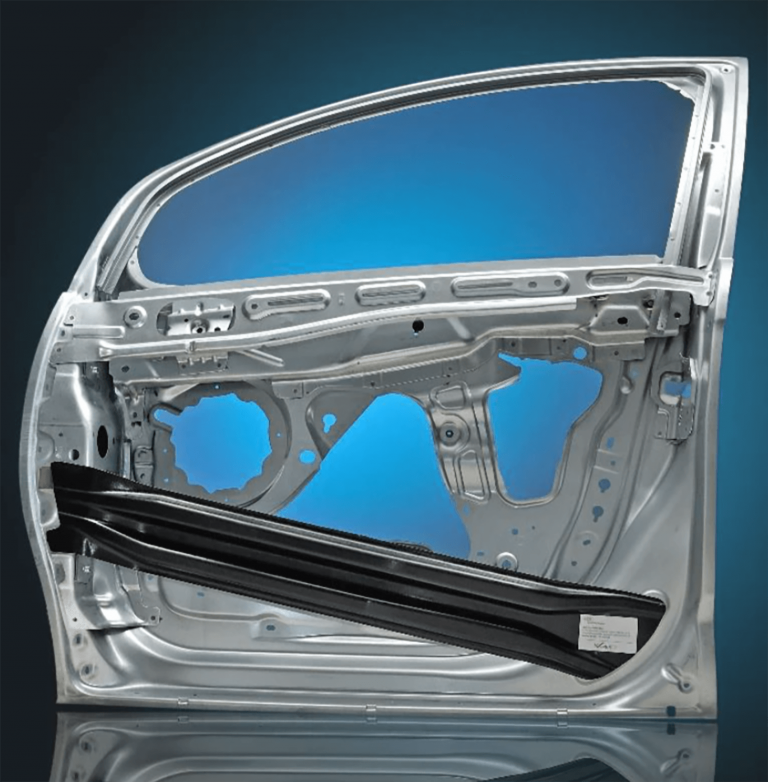
Рис. 1 Дверь автомобиля, армированная стеклопластиком
С появлением легковых автомобилей широкое распространение получили металлические и пластиковые соединения.
Как быстро и эффективно соединить металл и пластик, содержащий армированное углеродное волокно или стекловолокно, такого рода проблема срочно нуждается в решении.
Для того чтобы соответствовать требованиям работы сборочных линий в автомобильной промышленности, процесс соединения должен быть быстрым, надежным и автоматизированным.
Ниже приведен список из трех наиболее распространенных способов соединения композитных и металлических деталей в промышленности.
Среди них лазерная технология соединения является новейшей технологией.
Многие проблемы еще предстоит решить в этой технологии.
Эти проблемы связаны не только с эффективностью, но и с прочностью суставов и старением.
В этой статье мы подробно обсудим эти проблемы.
1) Механическое соединение
Это быстрый, экономичный и стабильный процесс.
Недостатком является то, что отверстия в композите разрушают распределение волокон и прочность композита.
Соединители, такие как винты, увеличивают вес сборки.
2) Склеивание
Существует широкий выбор клеев для соединения различных материалов.
Недостатки заключаются в том, что поверхность нуждается в предварительной обработке, процесс склеивания занимает много времени, необходим клей, а стоимость увеличивается.
3) Лазерное соединение
Он быстр и надежен, с высокой прочностью соединения, и ему не нужен никакой вспомогательный материал.
Но его недостаток заключается в том, что он применим только к термопластам.
1. Основы технологии лазерного соединения
Лазерное соединение термопластичных и металлических деталей делится на два этапа.
На первом этапе микроструктура формируется на поверхности металлических деталей путем лазерной обработки.
Обычно это делается с помощью волоконного лазера мощностью 1 кВт.
Лазер сканирует поверхность и обрабатывает правильную канавку и подрезанную структуру (рис. 2).
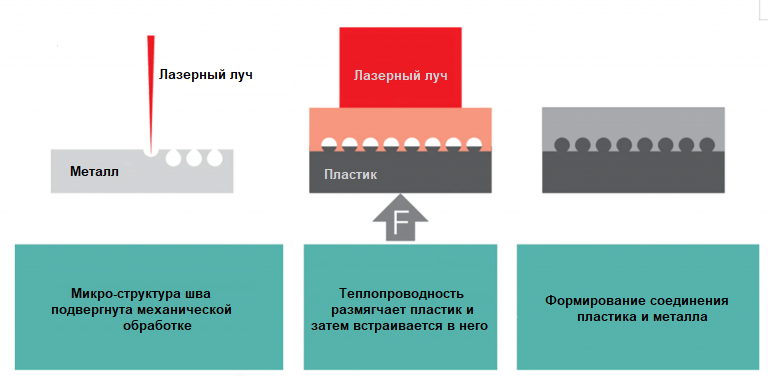
Рис. 2. Процесс лазерного склеивания пластика и металла
Из-за высокой плотности мощности лазерного луча металл частично расплавляется и испаряется.
Расплавленный металл выбрасывается испарением под высоким давлением, и часть его затвердевает на краю канавки, образуя подрезанную структуру.
Чтобы максимально увеличить сцепление пластика с этой поверхностью, количество и плотность канавок можно увеличить, как показано на рис. 3.

Рис. 3. Несколько сканирований лазерного луча для получения хорошей формы канавки
Существует альтернатива, которая реализуется с помощью специального импульсного ультракороткоимпульсного лазера (ИУЛ) для формирования губчатой поверхности с коническим выступом.
Его можно использовать на стальных, алюминиевых, кремниевых и титановых поверхностях.
На такой поверхности сила сцепления пластмасс даже лучше, чем у микроструктуры, обработанной волоконным лазером.
Единственная проблема заключается в том, что ИУЛ-лазер слишком медленный.
На этапе 2 пластик нагревается до расплава, а затем вдавливается в металлическую поверхность.
После охлаждения пластик соединяется с металлом.
Существует множество способов нагрева пластмасс.
Один из методов заключается в том, чтобы нагревать пластик непосредственно, используя горячую пластину, инфракрасное излучение и другие процессы, а затем вдавливать его в канавку металлической поверхности.
Другой способ нагреть металлические детали и прижать их к холодному пластику.
Теплопроводность заставляет пластик плавиться, а затем перетекать в крошечные структуры металла.
На первом этапе лазерная микрообработка выполняется быстро и бесконтактно.
Поэтому этот процесс очень подходит для вставки в существующий производственный процесс и подходит для массового производства.
2. Испытание на прочность соединения
В практическом применении соединение между металлом и пластиком будет нагружено.
Итак, каково же максимальное давление такого рода композитного соединения? Где он сломается?
Специалисты из Научно-исследовательского института лазерной технологии Hoff в Германии провели серию стресс-тестов на различных материалах и ответили на эти вопросы (рис. 4).
Одно из содержаний теста выглядит следующим образом:
Были проведены испытания на сдвиг пластины из нержавеющей стали толщиной 1,5 мм и соединителя из полипропилена толщиной 3 мм со стекловолокном;
Было проведено испытание на растяжение пластины из нержавеющей стали толщиной 1,5 мм и соединителя из полипропилена толщиной 3 мм (исключая стекловолокно).
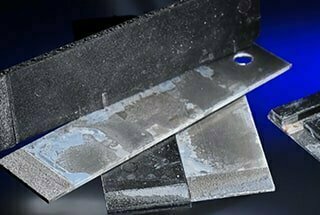
Рис. 4. Поверхность разрушения соединения металла и пластмассы после коррозионных испытаний
Одномодовый волоконный лазер мощностью 1 кВт используется для микрообработки металлической поверхности, а диаметр пятна составляет около 40 мкм.
Воспроизводимая структура подрезанной канавки создается на металлической поверхности лазером.
Пластик нагревается полупроводниковым лазером номинальной мощности 3 кВт с размером пятна 7,5 мм × 25 мм.
Зажмите две части с давлением 0,3 МПа.
Результаты таковы:
- Нержавеющая сталь + Полипропилен со стекловолокном, площадь соединения 150 мм2
- Нержавеющая сталь + Полипропилен, площадь соединения 100 мм2
Разрушающие испытания проводились на 5 образцах каждого из вышеперечисленных двух типов.
Для нержавеющей стали + Полипропилен со стекловолокном было проведено испытание на прочность на сдвиг.
- Когда расстояние между пазами составляет 400 мкм, максимальная нагрузка на сдвиг составляет 13,1 Мпа;
- Максимальная нагрузка на сдвиг составляет 15,5 Мпа при расстоянии между пазами 300 мкм.
Для нержавеющей стали + ПП было проведено испытание на прочность на растяжение.
- Максимальная растягивающая нагрузка составляет 5,1 Па при расстоянии между пазами 400 мкм;
- Максимальная растягивающая нагрузка составляет 9,1 Мпа при расстоянии между пазами 300 мкм.
Очевидно, что плотное распределение канавок полезно для повышения прочности соединения.
Однако следует отметить, что плотные канавки увеличат время микрообработки.
В то же время аналогичный эксперимент был проведен на магниевом листе.
Все испытания показали, что лазерная технология склеивания создает прочное и надежное соединение между металлическими и пластиковыми деталями.
3. Испытание на старение
Еще один важный вопрос автомобильной продукции:
Соответствует ли это соединение требованиям устойчивости к изменению климата и коррозионной стойкости?
Чтобы ответить на этот вопрос, специалисты из Института лазерной технологии Хоффа в Германии провели и другие испытания.
В эксперименте различные металлы (сталь и алюминий) и различные пластмассы (ПП + 30% стекловолокна и ПП + 40% талька) были соединены вместе лазером.
Стандарт VW PV 1200 был использован для испытания на изменение климата, а диапазон температур составлял 80 ℃ ~ 40 ℃.
Один тестовый цикл составляет 12 часов, который необходимо повторить дважды, 10 и 30 раз соответственно.
До и после испытания испытывали разрушающую прочность образца на сдвиг.
Все результаты испытаний были распределены между 8 и 15 МПа.
В тесте также есть интересное явление: После 30 циклов испытаний все образцы ПП, заполненные порошком талька, треснули вне зоны соединения при испытании на прочность.
Другими словами, соединение прочнее, чем объемнее полипропилен.
Аналогичное явление наблюдалось и при испытании на коррозионную стойкость.
Испытание проводилось по стандарту VDA 621-415 в течение 7 дней.
Испытание включает в себя соленые брызги и условия испытаний с высокой влажностью.
Перед испытанием все образцы выдерживают прочность на сдвиг 8-5 Мпа.
Испытание на сдвиг проводилось после коррозионного испытания, и все образцы ПП, содержащие порошок талька, трескались вне зоны соединения.
Образец ПП, содержащий стекловолокно, ломается в области соединения, но его прочность выше, чем у образца до испытания.
Коррозия нержавеющей стали происходит, особенно в микроструктуре.
Зона лазерного склеивания также имеет очевидное проникновение коррозии, но не оказывает очевидного влияния на прочность склеивания. Есть также признаки коррозии в микроструктуре вне зоны соединения, но не внутри зоны соединения.
Поэтому можно сделать вывод, что микроструктура не должна находиться в открытой среде.
4. Заключение
Метод лазерного соединения металла и пластика был испытан и доказал свою способность производить высокопрочное и надежное соединение.
Климатические и коррозионные испытания не влияют на прочность соединения.
После некоторого старения местом излома является пластиковый корпус, а не место соединения.
Контакты
Телефон | +7(495)797-78-97 |
Адрес | ООО "АрматА", ИНН 7721482360, г. Москва, Рязанский проспект, д. 86/1 |
info@fiber-laser.ru | |
Доп. поле | Авторизованный дилер RayTools AG на территории РФ |
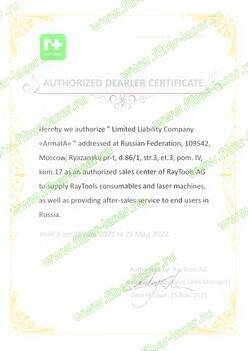